Root Cause Analysis (RCA) is invaluable for organizations across various industries, from manufacturing and healthcare to IT and business management. At its core, RCA seeks to identify the fundamental causes of problems or failures, ensuring that they do not recur. However, RCA is often perceived as a daunting task due to its complexity and resource demands. This comprehensive blog explores three robust strategies to simplify root cause discovery and analysis, making it more accessible and effective for sustained organizational improvement.
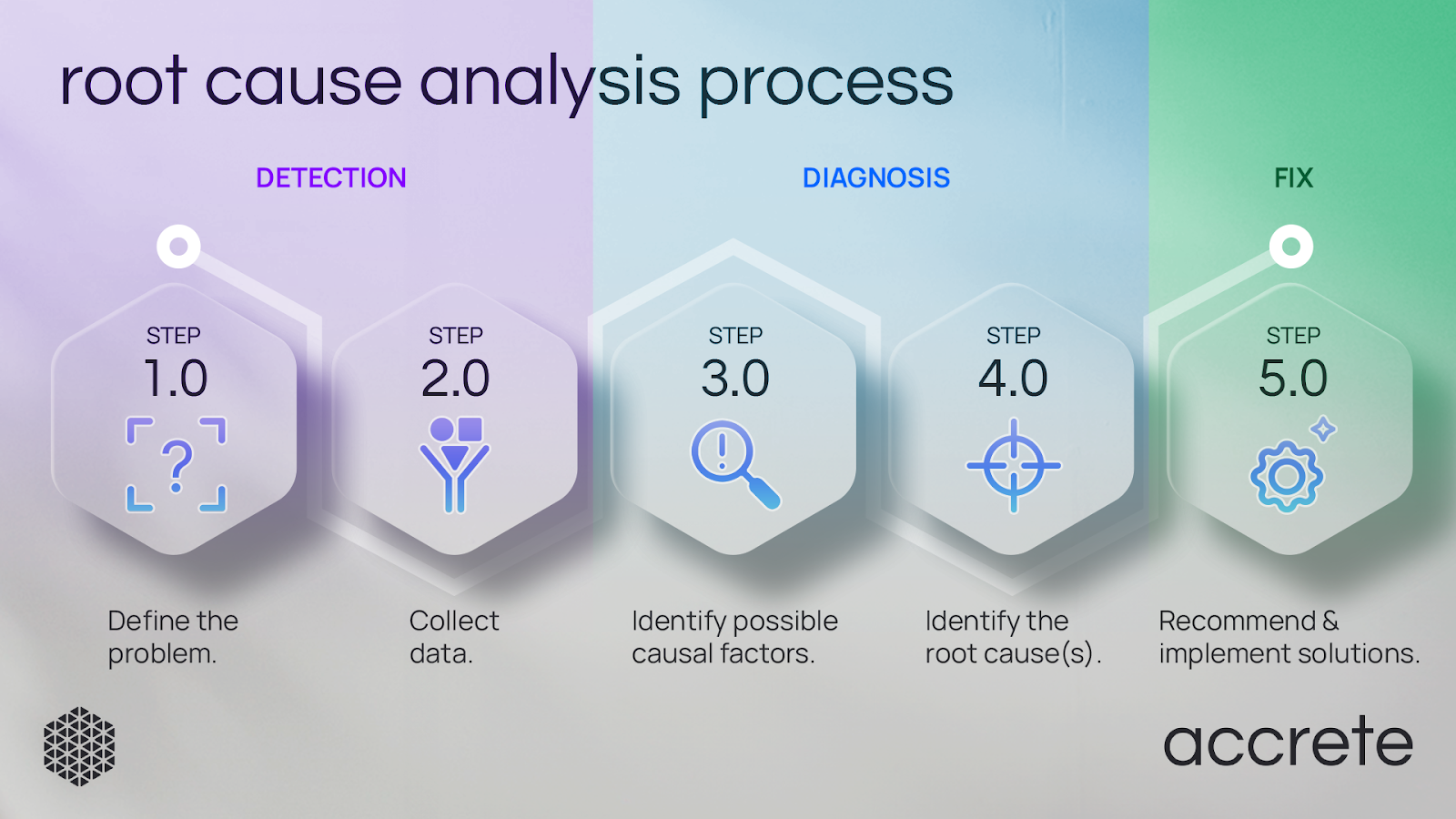
The Root Cause Analysis Process
IT teams typically perform root cause analysis (RCA) for critical incidents or unplanned outages using these three key phases:
1. Detection Phase
During this crucial first phase, the IT team becomes aware of and defines the problem. This involves:
- Identifying that an incident or outage has occurred, often through monitoring systems, user reports, or automated alerts
- Gathering initial information about the scope and impact of the issue
- Understanding which systems, services, or users are affected
- Documenting when the problem started and any immediately observable symptoms
- Creating an incident ticket to track the investigation
- Notifying relevant stakeholders based on the severity of the incident
2. Diagnosis Phase
This investigative phase is where the team digs deep to understand the true source of the problem. The diagnosis process typically includes:
- Collecting detailed system logs, error messages, and performance metrics
- Analyzing data patterns and system behavior leading up to the incident
- Tracing the sequence of events that preceded the outage
- Interviewing relevant team members or users who first noticed the issue
- Creating a timeline of events to understand the incident's progression
- Using tools like log analyzers, monitoring systems, and debugging tools
- Testing hypotheses about potential causes in a controlled manner
- Identifying any contributing factors or conditions that led to the incident
3. Fix Phase
The final phase focuses on resolving the incident and preventing future occurrences:
- Developing and implementing an immediate solution to restore service
- Testing the fix to ensure it fully resolves the issue
- Documenting the resolution steps taken
- Creating a detailed post-mortem report of the incident
- Implementing preventive measures to avoid similar incidents
- Updating monitoring systems and alert thresholds as needed
- Revising relevant procedures or documentation based on lessons learned
- Conducting a review meeting with stakeholders to share findings
- Creating action items for long-term improvements
What makes this process particularly effective is its systematic approach to problem-solving. The team moves from identifying the immediate symptoms (Detection) through understanding the underlying causes (Diagnosis) to implementing both immediate and long-term solutions (Fix). Each phase builds upon the information and insights gained in the previous phase.
3 Ways to Simplify and Streamline Root Cause Analysis Process
1. Adopt a Structured Methodology
One of the principal ways to simplify root cause discovery is by adopting a structured methodology. A well-defined framework provides a roadmap that guides individuals through the analysis process, ensuring consistency, thoroughness, and accuracy. Several established methodologies, each with its unique strengths, can be considered.
The Five Whys Technique
The Five Whys is a straightforward yet powerful tool grounded in lean principles. The technique involves persistently asking "Why?" until the root cause of a problem is uncovered. Here's a more detailed approach to effectively applying this technique:
- Problem Statement: Clearly and concisely articulate the problem. The problem statement should be specific, measurable, and observable.
Example: "The manufacturing line has frequent stoppages." - First Why: Ask, "Why did this problem happen?" Identify the immediate cause without jumping to conclusions.
Example: "Why did the manufacturing line stop?" Answer: "The conveyor belt malfunctioned." - Subsequent Whys: Continue asking "Why?" for each answer provided. delve deeper into each layer of cause, ensuring each "Why" digs deeper into the chain of events.
Example: "Why did the conveyor belt malfunction?" Answer: "The motor overheated." - Verify and Validate: Once you believe you've reached the root cause, verify it by checking against available data, expert judgments, and additional test cases if necessary.
Ask, "Why did the motor overheat?" Answer: "There was a lack of maintenance." Continues to "Why was there a lack of maintenance?" to finally, "Why was the maintenance schedule not followed?" - Implement Corrective Actions: Once the root cause is identified and confirmed, develop a clear action plan to prevent recurrence.
Example: "Implement a robust, monitored maintenance schedule."
By persistently asking "Why?" you can drill down through the symptoms to uncover the actual root cause. This iterative questioning method is incredibly effective for identifying the layers of causes that culminate in the observable issue.
Fishbone Diagram Methodology (Ishikawa)
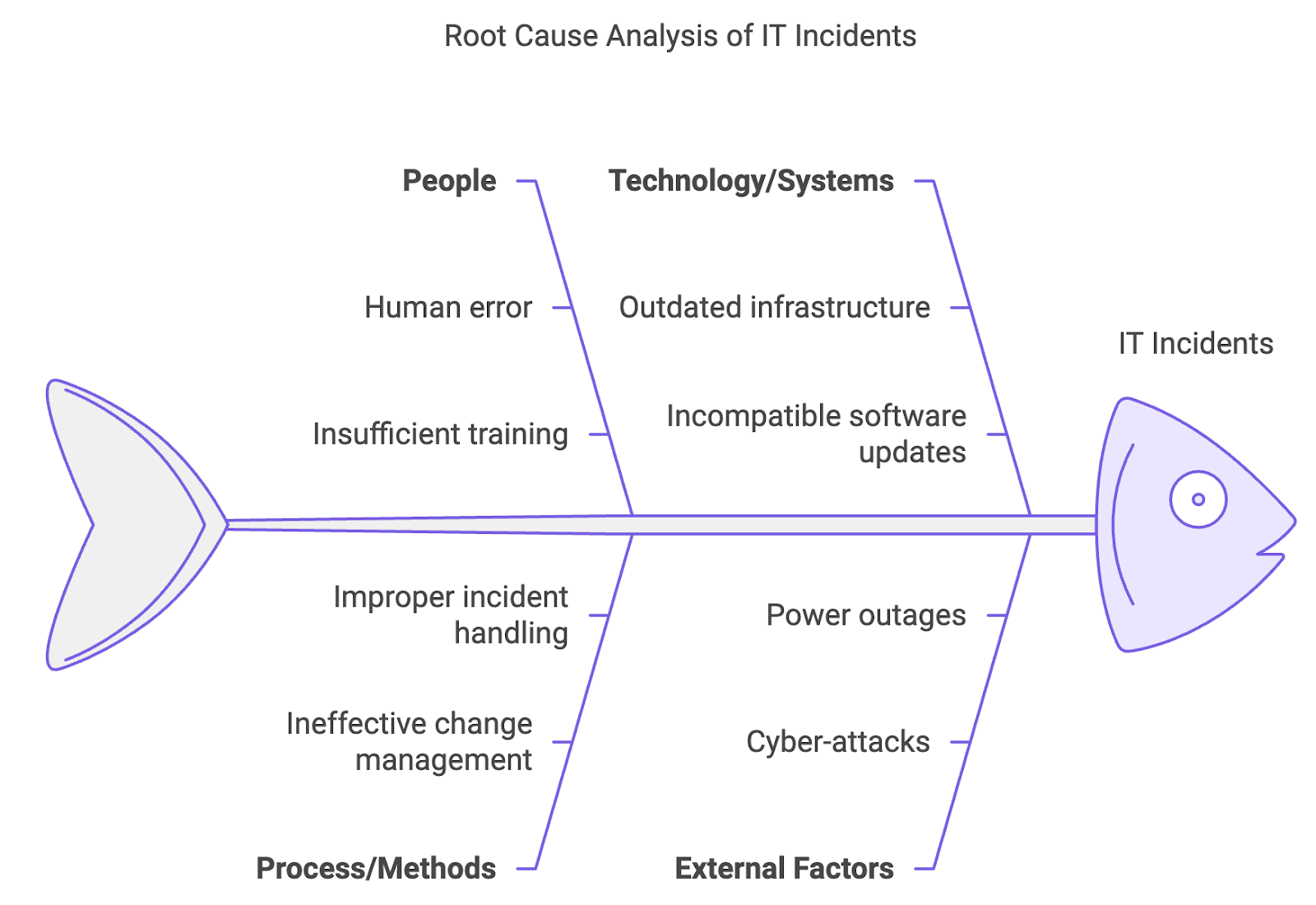
Named after its inventor, the Fishbone Diagram helps visually map out various potential causes of a problem. It categorizes causes into major branches—typically people, processes, equipment, materials, environment, and management—and systematically explores their contributions.
- Draw the Fishbone: Write the problem statement at the head of the diagram. The backbone leads to the main problem or effect.
Example Problem Statement: "Frequent Product Defects." - Identify Categories: Draw major branches to represent different categories of potential causes—people, processes, equipment, materials, environment, and management.
Example: "Each branch maps out specific aspects of the process contributing to defects." - Brainstorm Causes: Working through each major category, brainstorm all possible causes. Use brainstorming sessions with cross-functional teams to ensure a well-rounded perspective.
Example: "Under 'Equipment,’ list causes like 'old machinery,' 'lack of maintenance,' 'wrong settings. " - Analyze and Verify: Investigate each identified cause to confirm its contribution. Validate through data, expert consultations, and trials.
Example: "Old Machinery" checks frequency of malfunctions, replacement cycles, maintenance logs." - Prioritize and Address: Rank the identified causes based on their impact and feasibility of corrective measures. Implement the changes systematically
This visual representation helps clarify complex problems and identify areas needing further investigation, particularly useful for tackling more intricate problems with multiple contributing factors..
2. Leverage Technology and Tools
Advancements in technology can tremendously simplify RCA by providing tools and systems that automate data collection, analysis, and visualization.
Data Analytics Platforms
Modern data analytics platforms can sift through vast amounts of data to uncover patterns and anomalies that may not be immediately apparent. These platforms offer real-time insights, making it easier to identify root causes. By harnessing the power of big data, organizations can make more informed decisions backed by empirical evidence rather than conjecture.
- Automated Data Collection: Use IoT devices and sensors to gather data in real-time, ensuring accuracy and comprehensiveness.
- Anomaly Detection: Incorporate machine learning algorithms to detect patterns and anomalies in vast datasets, ensuring no stone is left unturned.
- Dashboards and Visualization: Utilize advanced visualization tools to create intuitive dashboards that simplify data interpretation and highlight critical insights.
Artificial Intelligence and Machine Learning
AI and ML algorithms, such as the ones leveraged in Accrete AI’s platforms, can predict potential causes based on historical data and trends. These technologies can analyze numerous variables and data points, making RCA faster and more precise.
- Predictive Modeling: Develop models that predict potential issues before they occur, based on past trends and real-time data. Read Accrete’s E-book on an Introduction to Pre-Change AIOps to learn how predictive modeling for IT Change management helps to prevent unplanned downtime.
- Adaptive Learning: Use machine learning to adjust and refine algorithms continuously, improving the accuracy and reliability over time and use.
- Root Cause Prediction: AI can sift through historical incident logs and current data to suggest probable root causes, reducing the manual burden.
Predictive analytics, for example, can anticipate failures before they occur, reducing downtime and identifying underlying issues proactively. Machine learning can continually adapt and improve its predictions as more data is fed into the system, enhancing the sophistication and accuracy of root cause identification over time.
Collaborative Tools
Collaborative tools facilitate communication and ensure that all stakeholders are engaged in the RCA process. Real-time communication and shared documentation ensure that information flows seamlessly, avoiding miscommunication and ensuring a unified approach.
- Real-Time Collaboration: Use project management tools and platforms (e.g., Asana, Trello) to foster real-time collaboration among team members.
- Shared Documentation: Cloud-based document sharing tools ensure all team members can access, edit, and update RCA findings and plans seamlessly.
- Integrated Communication: Use integrated communication platforms like Slack or Microsoft Teams for instantaneous information sharing and status updates.
Project management platforms, shared digital workspaces, and instant messaging solutions keep the entire team on the same page. Integration with existing systems and workflows enhances efficiency and ensures that no data is lost or overlooked at any stage of the RCA process.
3. Foster a Culture of Continuous Improvement
The most effective RCA isn’t just a one-time exercise—it’s an ongoing commitment. Cultivating an organizational culture that values continuous improvement can significantly simplify root cause discovery.
Employee Training and Empowerment
Equip employees with the skills and knowledge needed to conduct effective RCA. Regular training sessions and workshops can make methodologies like the Five Whys or Fishbone Diagram second nature.
- Comprehensive Training Programs: Implement regular training sessions covering the fundamentals of RCA methodologies, data analytics, and problem-solving techniques.
- Skill Development Workshops: Facilitate hands-on workshops where employees can practice RCA in simulated or real-world scenarios.
- Empowerment Initiatives: Encourage employees to take ownership of RCA activities, fostering a proactive problem-solving culture.
Empowering employees to ask the right questions and seek out improvements proactively builds a robust problem-solving culture. When employees are confident in their RCA abilities, the quality and speed of root cause discovery increase dramatically.
Document and Share Lessons Learned
Create a centralized repository where all RCA findings are documented and accessible. Sharing these insights across the organization prevents repetition of past mistakes and fosters a culture of transparency and learning.
- Central Knowledge Base: Develop a centralized digital repository where RCA findings, corrective actions, and lessons learned are stored and easily accessible.
- Systematic Documentation: Standardize the documentation process to ensure consistency and comprehensiveness across all RCA activities.
- Internal Sharing Programs: Implement programs to regularly share key insights and improvements derived from RCA across the organization.
A well-maintained knowledge base serves as a valuable reference, enabling teams to build upon previous work and continuously refine their problem-solving techniques. It becomes a living document that evolves with the organization, offering historical context and practical insights for future RCA activities.
Encourage a Blame-Free Environment
A culture of continuous improvement thrives in a non-punitive environment. Encourage employees to report issues without fear of reprisal. When problems are seen as opportunities for improvement rather than failures, employees are more likely to engage in the RCA process actively and willingly.
- Non-Punitive Policies: Clearly communicate policies that encourage reporting and open discussions about issues without fear of blame or punishment.
- Recognition Programs: Acknowledge and reward employees who actively participate in RCA and contribute to meaningful improvements.
- Open Communication Channels: Foster open and transparent communication where employees feel safe sharing insights, ideas, and concerns.
Promote a mindset where failure is viewed as a learning opportunity. Recognize and celebrate instances where root cause identification has led to significant improvements. This positive reinforcement encourages a proactive approach to problem-solving and continuous learning.
Root Cause Analysis is a powerful tool for diagnosing issues and implementing lasting solutions. By adopting structured methodologies, leveraging modern technology, and fostering a culture of continuous improvement, organizations can simplify and enhance the RCA process. Streamlining RCA not only improves problem-solving capabilities but also drives innovation, efficiency, and excellence across all operations.
Embrace these strategies, and you will transform challenges into opportunities for sustained growth and success. Root cause discovery doesn't have to be a daunting task. With the right approach, it can become a straightforward, insightful, and, ultimately, transformative process that propels your organization towards excellence. By investing in structured methodologies, advanced technologies such as Accrete AI’s Nebula ITSM tool for automating RCA, and a culture that prioritizes continuous improvement, your organization will be well-equipped to navigate and resolve any challenges that arise, turning potential setbacks into opportunities for growth and development.